The Europa uses two different epoxies. Laminations are done using Aeropoxy PR 2032, and structural bonds are done using Araldite 420. The latter is also sold as Epibond 420 in the U.S. It is a pretty useful product not just for aircraft, but also as a general high strength adhesive. I’ve used it in my laboratory for a variety of needs.
The cost of Araldite 420 has gone up significantly in recent years (over $600 a quart). This is because heavy industries like Boeing have started to use this adhesive in their products. I had three quartz of Araldite 420 that was more than 20 years old, so it was unclear if it was still usable. It’s published shelf life is very short (12 months, I think). Usually, the expiration date is when the manufacturer will dispose their records, so it does not necessarily mean the product won’t work. But it was still important to find out.
Mixing ratio of the resin and hardener of Araldite 420 is 1:0.4. The mixing ratio of the Aeropoxy PR 2032 is 1:0.27. I had a nagging doubt if some of the Araldite 420 bonds I had done years ago were mixed at the correct 1:0.4 or at the incorrect 1:0.27. So I decided to test both.
Sample Preparation
I bought a small 50ml cartridge of brand new Epibond 420 for comparison. Interestingly, this did not have an expiration date printed. The test coupons were prepared using 1″ x 6″ aluminum plates. After scuff sanding and rinsing with acetone to remove any oils, two plates were overlapped by one square inch area and were bonded together. They were held with C-clamps during cure. Testing was conducted roughly 2-3 weeks after the bonding.
Eight test coupons were prepared as listed below:
- Expired Araldite 420 mixed at the recommended ratio of 1:0.4 (two samples)
- Expired Araldite 420 mixed at the incorrect ratio of 1:0.27 (two samples)
- Brand new Epibond 420 mixed at the recommended ratio of 1:0.4 (two samples)
- Aeropoxy PR 2032 mixed at the recommended ratio of 1:0.27 (two samples)
Test Results
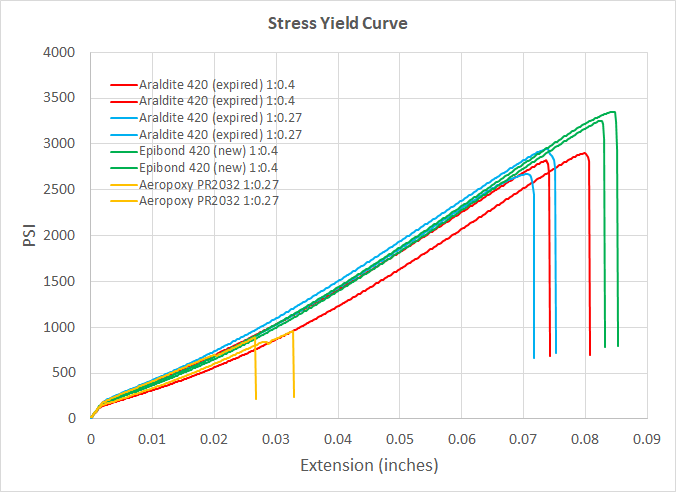
The tests were run at one of my colleagues materials testing laboratory.
The spec sheet for the new Epibond 420 states a lap shear strength of 3500 psi. My results were in the range of 3250-3350 psi, which is slightly lower than the spec. I could not find any specifications for the Araldite 420 manufactured circa 2000, but my measurement data was in the range of 2800-2900 psi. The lower number could be due to its age, or it could also be due to an older formulation used in the Araldite 420. In any case, the difference is only 15%. I do not believe this is a significant difference, and gives me confidence that it is still usable.
A more surprising result is the mixing ratio. When the Araldite 420 was mixed at 1:0.27, the resulting strength showed no noticeable difference. The lap shear strength was in the range of 2650-2950 psi.
Finally, I also tested Aeropoxy PR 2032. It’s lap shear strength was significantly lower, at 850-900 psi. This is the expected result because it is a laminating epoxy and not a structural epoxy.
Failure Modes
The images below show the bond interfaces after the separation. All of the failures seem to have occurred at the epoxy/aluminum interface, and it was roughly split in equal amounts from both interfaces. This result was fairly consistent across all samples. From this observation, I concluded that the weakest part of the bond is the interface. That means, better surface preparation could result in a higher shear strength.
![]() Araldite 420 (expired) 1:0.4 Sample #1 | ![]() Araldite 420 (expired) 1:0.4 Sample #2 |
![]() Araldite 420 (expired) 1:0.27 Sample #3 | ![]() Araldite 420 (expired) 1:0.27 Sample #4 |
![]() Epibond 420 (new) 1:0.4 Sample #5 | ![]() Epibond 420 (new) 1:0.4 Sample #6 |
![]() Aeropoxy PR2032 1:0.27 Sample #7 | ![]() Aeropoxy PR2032 1:0.27 Sample #8 |
Leave a Reply